新聞資訊 |
|
 |
推薦產品 |
|
 |
|
|
|
|
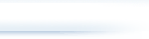 |
壓鑄技術的現狀及展望 |
發布日期:2011-02-14 10:01 |
摘要:從壓鑄件市場對企業和壓鑄件質量越來越高的要求和當前壓鑄業現狀及發展趨勢,提出我國壓鑄行業發展的方向及要點。
關鍵詞:壓鑄技術 壓鑄設備 壓鑄合金 計算機模擬
前言
壓力鑄造自本世紀40 年代問世以來,作為一種金屬零件接近最后形狀尺寸的精密加工工藝,其發展方興未艾。在壓鑄設備及其控制、壓鑄工藝及壓鑄合金等方面不斷取得新的進展。同時市場需要大量生產復雜薄壁和美觀的金屬零件,滿足當今汽車工業、電子通訊和家用電器、玩具等產業對壓鑄件越來越高的要求。但由于壓鑄件一些固有的問題未得到徹底解決,合金的潛能未得到充分發揮。壓鑄業還面臨進一步提高技術和管理水平以保證鑄件的高質量和低成本的任務。
當前的市場是動態的市場,要在競爭中立于不敗之地,企業必須能夠及時調整自己的經營策略,這要建立在先進的技術和管理的基礎之上。技術創新將要成為21 世紀企業競爭的焦點。只有將關鍵的技術掌握在自己手里和采用先進的管理體制,才能提高對動態多變市場的響應速度,提高企業的競爭能力。
當前廣東省乃至全國的壓鑄業,離國際先進水平尚有很大差距。自改革開放以來,從香港遷入廣東的與壓鑄有關的企業有幾百家。所以,近十多年來,廣東壓鑄業得到飛速的發展[1 ] 。據不完全統計,全省有一定規模的壓鑄廠家超過600 家,年產壓鑄件3 000~5 000 t 的廠家有8 家以上,1 000~3 000 t 的廠家有10 多家,500~1 000 t 的有幾十家。年產鋅合金壓鑄件接近10 萬t ,鋁合金壓鑄件約4 萬t 。全省擁有壓鑄機約2 000 多臺,最大的是21 000 kN 合模力的意大利壓鑄機。全省有壓鑄機制造廠7 家,壓鑄周邊設備生產廠有10 多家。年產壓鑄機約600 臺,絕大部分為熱室機。主要存在下述幾個問題:壓鑄設備以小型為主,控制系統都比較落后;壓鑄件以鋅合金為主,多為家電、玩具等非受力零件,汽車、摩托車等零件比重還比較少;模具制造是個薄弱環節,模具廠家不少,但多是小規模的,設備比較落后,生產周期長,只有個別模具廠開始實施CAD/ CAM 技術。要使我國的壓鑄行業達到世界先進水平,還有一段相當長的路要走。必須推行壓鑄技術創新工程;開發新的壓射系統和控制系統;提高壓鑄件的內在質量;發展新的壓鑄技術;研究新的壓鑄合金材料;實行現代化管理。
1 開發新的壓鑄設備及其控制系統
壓力鑄造是使金屬液在高壓條件下以極高速度充填型腔的過程,是一個復雜的動態熱力學過程。一方面,壓鑄可以生產出復雜薄壁、表面美觀和高精度的金屬鑄件。而另一方面,一般壓鑄過程難于達到層流充填狀態而卷入氣體和夾雜物,得不到致密、可熱處理的工件,影響了它的力學性能。如果用降低充填速度這種手段來改善金屬液的充填狀態,又勢必犧牲上述壓鑄生產所帶來的優勢,且對復雜薄壁零件不一定有效。而生產高質量、無氣孔的薄壁壓鑄件卻又是我們追求的目標,這是壓鑄工藝其他工藝競爭時賴以取勝的籌碼之一。
為了提高競爭力,薄壁這個指標也在不斷推高,它是一個非常柔性的指標。如50 年代汽車工業的薄壁車身是2 mm ,現在已是0. 7 mm ,到2000 年將是0. 5 mm。鋅壓鑄件所指薄壁,60 年代為2 mm ,70 年代為1 mm ,80 年代為0. 7 mm ,90 年代為0. 3~0. 5 mm。鋁壓鑄件有類似的發展,90 年代為0. 5~1 mm。
致密薄壁鑄件是以足夠的金屬壓力和短的充填時間為條件的,也就是在一個極短的時間內以高的內澆口流速和足夠的金屬壓力進行充填。這就要求壓鑄機在既能產生高的壓射速度的同時又能產生高的金屬壓力。即根據鑄件工藝要求,壓鑄機要能提供一定的壓射能量,以便能夠實現高能充型。要得到0. 75 mm 以下壁厚的致密鑄件,就需要壓射能量在550 kW·h 以上的壓鑄機。
高能充型還能調節各種工藝參數,得到高質量的壓鑄件。高能充型是壓鑄機壓射系統的發展方向。一臺壓鑄機要達到高的充型能量,就要盡量減少各種摩擦阻力和局部阻力以及慣性力所造成的能量損失———壓力降。
另外,壓鑄機的先進性主要體現在生產過程中的穩定性和可再現性,即每次壓射盡可能接近預先設定的理想的壓射曲線。但在壓鑄過程中存在很多變量影響壓鑄過程的穩定性[2 ] 。壓鑄機和模具的工作狀態、儲能器壓力等靜態因素在工藝設備選定之后是不可改變的。
而一些動態因素和人為因素所引起的變量(如每次壓射的金屬量及其溫度、模具溫度、液壓油粘度、涂料的噴涂質量、人為設定的參數等等) 必須通過壓射控制系統進行修正。一次壓射時間平均需20~80 ms ,薄壁鋁合金或鎂合金件要求的充填時間更短,為5~12 ms[3 ] ,壓射控制系統必須能夠以只相當于一次壓射所用時間的10 %左右,即2~8 ms 的響應時間來控制壓射曲線。這對電子線路系統就提出了嚴峻的要求,即電子線路控制系統必須在幾微秒內作出反應。可再現性要求高,就要安裝金屬前沿傳感器[4 ] 。在金屬液封住傳感器時,金屬液的前沿被精確地辨認出,信息反饋到電子控制設備,電子儀器重新計算,可以得到穩定的最佳壓射曲線。先進的傳感器的發展推動著壓鑄機及壓鑄工藝的發展。壓鑄件的組織和性能取決于壓鑄型腔內及其鄰近區域的熱物理條件,所以發展靠近型腔的熱探測器和傳感器有重要意義。
2 發展新的壓鑄技術
2. 1 半固態合金壓鑄
半固態合金同全液態和全固態合金相比,其物理性能有兩個特點。一是這種半固態合金的固態組分超過50 %之后,隨著固態組分的增加,其粘度急劇增加。而對未經攪拌的合金來說,固態組分超過15 %左右之后,其粘度就隨固態組分的增加而急劇增加。二是這種受激烈攪拌的合金具有攪溶性。
正是由于這種受激烈攪拌的半固態合金具有這種特殊的物理性能,所以它的鑄造性能優良,在固態組分比較高的情況下,它的流動性還相當好,比起全液態合金并沒有嚴重下降。另外,補縮性能也比較好,一方面其本身收縮量已減少,另一方面還可通過液2固兩相同時流動而補縮。又由于這種合金具有攪溶性,因此用于成型時受到很大剪切作用的壓鑄和擠壓工藝是比較合適的。比起全液態合金,半固態壓鑄更有其獨特之處。
一是全液態合金操作起來很不方便,這對改善工作條件和提高機械化和自動化程度都是個障礙,而半固態合金只是在成型時才表現出象流體一樣的特性,在成型之前可以象固態一樣搬運,這對組織高度機械化和自動化生產非常有利。二是半固態合金壓鑄時,鑄型受熱狀態得到很大改善。一個原因是合金本身的溫度降低了,所含熱量已較少,半固態金屬從壓鑄到完全凝固所需要散出的熱量僅為過熱狀態金屬的一半左右。另一個原因是半固態合金進入型腔的模式不同,不流淌,紊流程度又低,基本上可達到全壁厚充填,對鑄型的熱沖擊很低,鑄型壽命得到提高。因此,半固態壓鑄對高熔點合金很有應用前景。
半固態合金也為以鑄造方法制造金屬基復合材料提供了有利條件。在半固態合金受激烈攪拌時加入非包覆非金屬顆粒以制備復合材料是一種比較簡便的方法。由于半固態合金存在固態初晶,可以防止非金屬顆粒的浮沉或凝聚,分布比較均勻。另外,非金屬顆粒受到激烈攪拌、摩擦,表面得到活化,使其和基體合金結合緊密。
盡管半固態合金鑄造的概念在70 年代初就為M.C. Flemings 等人所提出[5 ] ,但到目前為止半固態合金漿料如何有效地制取并進行成型還是個問題[6 ,7 ] 。應用起來受到限制,材料選擇受到限制,對工藝規范要求十分嚴格。特別是固、液相分數要精確控制,其偏差要求在±3 %的范圍內。為了達到半固態壓鑄的工藝要求,工藝裝備設計是個關鍵。H. Peng 等[6 ]提出了流變成型工藝(Rheomolding) ,原理是將液態金屬送入特殊設計的壓射成型機筒中,由旋轉的螺旋裝置施加剪切而使之冷卻成為半固態漿料,達到工藝要求后進行壓鑄成型,一臺機器完成兩個工序(生產漿料和壓鑄) 。溫度控制是個關鍵。N. Bradley 等人[8 ] 提出了觸變成型工藝(Thixomolding) ,它是將固態鎂金屬粒或碎屑送入螺旋壓射成型機中,在加熱和受剪切的情況下,金屬變成漿料并壓鑄成型。該工藝多了一個切碎工序。
2. 2 新的噴涂技術
脫模劑的噴涂與壓鑄件質量關系很大。脫模劑從噴射裝置噴出時如果是非霧化的或非均勻分散的,凝聚的液體要求更長時間的汽化,當這一過程未完成就合模并強行將金屬液壓入,將加速潤滑劑的汽化和形成更高的蒸氣壓,這往往是造成鑄件疏松的根源。
水基涂料對工藝要求很高。對模溫有嚴格要求,有一個“潤濕溫度”。模溫低于此限,涂料才能成膜。成分不同,“潤濕溫度”不同。涂料膜的厚度也要嚴格控制,太厚時冷卻慢,容易形成氣孔,鑄件表面也易起皺;太薄時易裂,鑄件表面起痕跡。水基涂料噴涂時冒煙,不利于環保。
金屬液澆入壓室時往往出現局部凝固現象,形成彌散激冷組織,沖入型腔后會明顯降低鑄件的力學性能。往壓室噴涂液態涂料也不能徹底解決問題。
為此,很多研究工作者都致力于開發固體潤滑劑或半永久性涂料。目標是提高鑄型壽命,防止焊合,提高鑄件質量,改善環境條件。
3 發展新的壓鑄合金材料
3. 1 金屬基復合材料(MMCs)
汽車的輕量化、降低油耗和排放以及提高性能以保證質量與安全是當今汽車工業發展的主要方向。在新材料中,金屬基復合材料由于具有高的比強度、比模量、耐磨和減摩性能,熱強性和低的熱膨脹系數,可望在今后汽車工業的發展中有重要的地位。特別是用鑄造工藝制造金屬基復合材料零件有一定優勢。工藝比較簡單,成本低,應用上的局限性小。已經做了很多開發研究工作。據David Weiss 等人報道[9 ] ,SiC 顆粒增強的鋁基復合材料壓鑄比較成功,充填性有時比一般鋁合金還好,表面質量令人滿意。所用工模具和一般鋁合金壓鑄的一樣。
鋅鋁合金基復合材料用于耐磨減摩材料有很好的前景[10 ] 。以ZA227 合金為基體,在熔融狀態下與石墨復合成均勻漿料,經擠壓鑄造成型。微觀結構表明,金屬2石墨界面結合良好,石墨分布均勻。這種材料在石墨質量分數低于5 %時的承載能力比青銅ZQSn62623 的高。線膨脹系數下降10 %以上。減摩性、耐磨性和相對抗咬合性都遠比基體合金ZA227 的好。
3. 2 壓鑄鎂合金
鎂合金被譽為90 年代以后的金屬[11 ,12 ] ,近年來發展很快。預計到2006 年北美產量將增加3 倍。汽車工業是鎂壓鑄件的最大用戶,市場占有率為80 %左右。
目標是進一步減輕汽車重量。美國通用汽車公司用壓鑄生產鎂合金汽車輪轂。日本輕金屬(株) 用充氧壓鑄生產的鎂合金輪轂比鋁輪轂輕15 %。估計到2000 年,象缸體、發動機罩、車頂板、門框、后艙蓋板、車輪等都將用鎂合金來壓鑄。電子設備方面,要求新的設計必須能抗無用信號干擾,應有屏蔽作用。鎂合金就有這個特性。如雷達定位器殼體用鎂合金代替塑料,重量相當,而強度、抗沖擊性能得到提高。
鎂合金之所以有廣泛的應用前景,是由于還具有以下優越性。
(1) 低密度(1. 8 g/ cm3 ) , 與很多工程塑料(1. 43g/ cm3) 差不多。與鋁合金相比有更高的比強度。
(2) 有良好的鑄造性能。
(3) 成本有競爭力,因鎂輕,鎂價是鋁價的1. 5倍時就有競爭力。
鎂的儲量豐富,每立方英里海水含600 萬t 鎂。我國遼寧大石橋市一帶的菱鎂礦占世界儲量的60 %以上,品位又高(40 %以上) ??蓮氖褂脽崾覊鸿T獲利。先前影響總成本的防腐問題已得到解決,研究表明抗蝕能力低是微量重金屬元素所致,達到一定純度時,其抗蝕能力就與鋁合金相當。
3. 3 高鋁鋅基合金( ZA) [ 13]
從1979 年開始,高鋁鋅基合金壓鑄就成了ZA 合金技術一個最具活力的方面。ZA 合金壓鑄為設計高強、耐磨和輕質鑄件以代替較重材料和成本較高的制造方法提供了唯一的機會。
ZA 類合金最突出的特點就是高的強度和優良的摩擦學特性。
高鋁鋅基合金的抗拉強度比鋁合金380 約高20 %~35 % ,比鎂合金AZ91 高50 %~70 %。壓鑄ZA28 的抗拉強度約為394 MPa , ZA212 為422 MPa , ZA227 為450MPa 。最新研究表明,薄壁壓鑄件的強度值比上述的還要高。所以ZA227 壓鑄件的比強度接近380 合金。在汽車工業有很大競爭力。
ZA 合金特別是ZA227 具有很高的耐磨性能,優于傳統的耐磨合金材料錫青銅和鋁青銅。其壓鑄件可以用于越野車絞盤的傳動裝置和其他零件。
ZA 合金還有一個很大的優點是熔化溫度低,耗能低,約為鋁合金的1/ 3。
ZA 合金的工藝性好,充填性能甚佳,壓鑄件壁厚可到0. 5~1. 0 mm??梢詽M足輕質鑄件要求。加工性能也十分優良,切削速度可以是鑄鐵的3~5 倍,刀具壽命得到延長。
4 提高對市場的快速反應能力,推行并行工程( CE) 和快速原型制造技術(RPM) [14 ,15]
4. 1 并行工程
近十年來在技術上迅速取得的進展,足以使壓鑄工業發生革命性改變。這些最新技術包括:改進的傳感器和控制系統,更快速而可靠的計算機和軟件,廣域的三維(3D)計算機輔助設計(CAD) 和分析能力,改進的電子數據交換和接口技術,以及快速原型制造技術。使用這些技術的最大優點是信息量得到擴大和并行使用。在產品設計階段就同時進行工藝設計,考慮產品整個生產周期的所有因素,大大縮短了產品投放市場的時間。
4. 2 快速原型制造技術
所謂快速原型制造技術,簡單地說就是將要制作的零件的三維CAD 數據在計算機上作出水平環切的數據資料,用激光按這些數據資料對模型材料(如光硬化性樹脂) 進行逐層掃描和固化,掃描完了,層疊起來的最終產物就是所要求的模型。
快速原型制造法,如立體印刷(Stereolitho graphy) 和分層實體制造(Laminated Object Manufacturing) 已應用于很多產品。過去,多半用于設計制造檢驗工具,現在的發展是為制造工模具鋪路。這使開發新產品更為迅速。
目前壓鑄工業主要用快速原型制造技術為重力鑄造(如砂型鑄造或石膏型鑄造) 制造鑄模,再用此鑄模澆注出要開發的樣板壓鑄件。也可以用快速原型制造技術直接制造壓鑄模具。但要考慮的問題是公差精度問題。CNC 可生產高精度的壓鑄模具,但周期長成本高。也許鑄造模具可以達到接近最后形狀,然后經加工達到最后公差。用快速原型制造技術開發新的壓鑄模是有前景的。
5 開展CAD/ CAE/ CAM系統的研究與開發
90 年代出現了第三代液壓驅動的壓鑄機,具有更大的功率和速度,有更高的精度和可靠性,盡管如此,生產高質量無孔的薄壁壓鑄件仍然十分困難。原因是還缺乏準確地預測熔融金屬在型腔中的行為。
隨著計算機在壓鑄過程中應用的深度和廣度的不斷增加,壓鑄中出現的問題應該可以得到逐步解決。
計算機在壓鑄過程中的應用,歷史不長,但進展很快。起初只能進行壓鑄工藝參數的選擇,澆注系統的設計。后來可以對壓鑄件進行凝固模擬,顯示鑄型的溫度分布,預測縮孔的位置和應力分布等。不久又發展到充填模擬,預測澆不到、冷隔和其他與充填有關的缺陷。由于計算機模型的改進和計算機硬件性能的提高,使得充填和凝固模擬更為精確和快捷。不但可以設計壓鑄模,并能形成圖形和指令,輸出到數控機床進行模具加工,初步建立了CAD/ CAE/ CAM系統。
為了使模擬結果更接近壓鑄過程的實際情況,使加工出來的壓鑄模能一次試壓成功。還需做很多工作。一方面通過對壓鑄過程了解的逐步深化,帶入更多的與之有關的物理量到計算機模型中。如最近考慮的[16 ] ,在壓射過程中,熔體在流動時剪切應力不可逆地將機械能轉變為熱能而使粘度下降,對補縮有利。充填模擬也會由于考慮背壓對充填模式的影響而更為準確。為充填模擬提供更精確的物理邊界條件,根據壓鑄機的機械參數及特性進行壓射曲線的預測,以避免充填時壓射沖頭速度超過其臨界速度和內澆口流速超過其最大值。
另一方面,由于壓鑄過程是在高壓高速下進行的,靜態的和動態的影響因素很多,因此還需要進行大量的基礎理論工作,建立起精確的數學模型以描述這個復雜的壓鑄過程系統。
6 推行計算機集成制造系統(CIMS)
實施CIMS 工程就是借助計算機網絡、數據庫集成各部門產生的數據,綜合運用現代管理技術、制造技術、信息技術、系統工程技術,將企業生產全過程中有關人、技術、設備及經營、管理四要素及其信息流、物質流有機地集成,并實現企業整體優化,解決企業參與競爭所面臨的一系列問題,以實現產品的高效、優質、低耗、上市快,使企業在競爭中立于不敗之地。CIMS 是贏得競爭的手段。
|
|
|